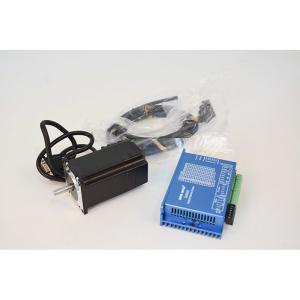
Add to Cart
2N.M Nema23 Closed Loop Servo Motor Integrated Digital Hybrid For CNC Router Milling Controller Kit
1. Product description
2.)The default work is in closed loop mode, no loss of step, and it also supports working in open loop mode.;
3.)Increase the output torque and running speed of the motor;
4.)The current level is intelligently adjusted according to the load, reducing the temperature rise of the motor, locking the current, and adjusting the closed-loop peak current.;
5.)Adapt to various mechanical load conditions (including low-rigidity loads such as pulleys and pulleys) without adjusting the gain parameters;;
6.)The position command smoothing filter can be set, the motor runs smoother, the vibration is lighter, and the acceleration and deceleration dynamic performance is improved.;
7.)Zero-speed static capability without vibration after positioning;
8.)Support single and double pulse input, pulse response frequency up to 200KHZ;
9.)Support 15 fixed subdivisions, and support software to set any subdivision (200~65535);
10.)Support modbus RTU protocol on RS232, position and speed control controlled by communication;
11.)Support monitoring of motor operating conditions, including speed, position deviation, bus voltage, operating current, etc.
12.)Voltage range: DC+24V~48V;
13.)With overcurrent, overvoltage, positional tolerance and other protection;
2-1 Electrical index
Power supply | DC36VRecommended power supply DC36V |
Output current | Peak 6.0A (current varies with load) |
Logic input current | 10mA7~16mA, recommended 10mA |
Pulse frequency | 0~200KHz |
Encoder line number | 1000 |
Insulation resistance | >=500MΩ |
2-2 Use environment and parameters
cooling method | Natural cooling or external heat sink | |
Use environment | Use occasion | Try to avoid dust, oil and corrosive gases |
Temperature | 0~40℃ | |
Humidity | 40~90%RH | |
Vibration | 5.9m/s2Max | |
Storagetemperature | -20℃~80℃ | |
weight | About1.3Kg |
2-3 Mechanical installation size
3. Typical wiring diagram
4. Drive interface and wiring introduction ( Interface definition )
4-1. Power input port
Terminal number | Symbol | Name | Description |
1 | +Vdc | DC power positive terminal | DC+24V~48V Recommended DC+36V power supply |
2 | GND | DC power ground |
4-2. Control signal port
Terminal number | Symbol | Name | Description |
1 | PUL+ | Pulse positive input | Support 5~24V |
2 | PUL- | Pulse negative input | |
3 | DIR+ | Positive input | |
4 | DIR- | Negative input | |
5 | ENA+ | Enable positive input | |
6 | ENA- | Enable negative input | |
7 | PEND+ | In-position signal positive output | OC gate output, the default closure indicates that the positioning is completed, and the open indication indicates that the positioning is not completed. |
8 | PEND- | In-position signal negative output | |
9 | ALM+ | Alarm signal positive output | OC gate output, the default close indication has an alarm signal, and the open indication indicates no alarm signal. |
10 | ALM- | Alarm signal negative output |
4-3. RS232 communication port
Terminal number | Symbol | Name |
1 | +5V | Positive power terminal |
2 | TXD | RS232 sender |
3 | GND | Power ground |
4 | RXD | RS232 receiver |
5 | NC |
4-4. Status indication
Steps / circle | SW3 | SW4 | SW5 | SW6 |
default | on | on | on | on |
800 | off | on | on | on |
1600 | on | off | on | on |
3200 | off | off | on | on |
6400 | on | on | off | on |
12800 | off | on | off | on |
25600 | on | off | off | on |
51200 | off | off | off | on |
1000 | on | on | on | off |
2000 | off | on | on | off |
4000 | on | off | on | off |
5000 | off | off | on | off |
8000 | on | on | off | off |
10000 | off | on | off | off |
20000 | on | off | off | off |
40000 | off | off | off | off |
The default file segmentation defaults to 400, which can be modified by the host computer software.